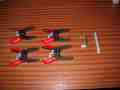
|
To build a hip assembly you will need two servo brackets, a length of
extruded aluminium tube (square profile), adhesive and thin polythene
sheet
Ensure that the adhesive is suitable for joining sheet steel to
aluminium and that it will NOT stick to polythene sheet plastic. If in
doubt perform a test.
Follow the adhesive manufacturers recomendations precisly. Pay special
attension to preparing the parts to be joined (in particular the
degreasing and no finger contact after preperation).
BEWARE: not all metal adhesives give good results. Some are MUCH better
than others, some will give extremely bad results. Try sticking a bad
bracket (one that you are not happy with and have discared) to some
aluminium tube, waiting for the recommended time then testing it to see
how well it performs. Test it by using the glued joint to lift weights,
start with small weights and gradually increase until the joint breaks.
This will give you a good indication of how strong the joint will be.
Check the broken joint. If the adhesive is still stuck to both parts on
coressponding areas then the adhesive has failed BUT it has stuck well
to both parts. If it supported several kilograms before failing then
this is a good adhesive and suitable for the purpose of building the hip
assembly. If the adhesive has only stuck to one part and not the other
(and you have prepared both parts as recommended by the manufacturer)
then look for an alternative adhesive
|
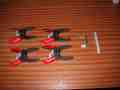
|
|
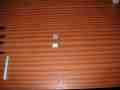
|
|
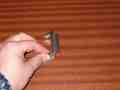
|
|
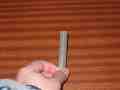
|
|
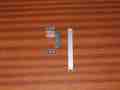
|
|
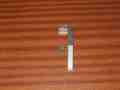
|
The bracket will be fitted to the aluminium tube as shown
|
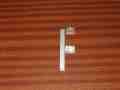
|
The work piece will be easier to handle if the bracket is resting flat
side down on the desk as shown.
Prepare the surfaces of both pieces at the points of contact. Follow the
adhesive manufacturers recommendations for preparing the surfaces.
|
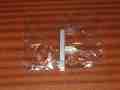
|
After covering the surfaces (at the point of contact only) with
adhesive, place a thin polythene sheet over the work piece. You will
also need to place a protective polythene sheet on your work surface
(none is shown here since it interfers with the photography).
|

|
Apply clamps to hold the two parts together until the adhesive has
cured.
NOTE the clamps are alternated between the top and side surfaces as
shown.
|
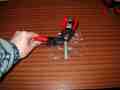
|
|
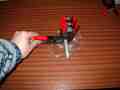
|
|
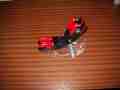
|
|
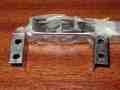
|
The adhesive will slowly cure until it becomes very hard. At some stage
the adhesive will become solid but not fully hard. Look for directions
on the adhesive packaging for information about this setting time.
Once the adhesive has reached this "not fully hard" state you should
remove the clamps and thin polythene sheet.
BEWARE: remove the clamps and sheet carefully and handle the work piece
carefully until the adhesive has fully cured. At this stage the joint is
weak and can easily be damaged or seriously weakend without showing
signs of damage.
|
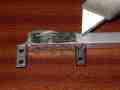
|
VERY carefully trim away any excess adhesive using a craft of hobby
knife.
Be carefull to hold the workpiece by the part you are cutting the
adhesive from. If you are cutting adhesive away from the backet then
hold the bracket. If you are cutting adhesive away from the tube then
hold the tube. Be careful not to push the blade between the bracket and
the tube.
|
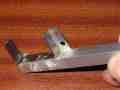
|
Pay careful attention to the part of the bracket shown. Too much waste
adhesive here can cause big problems with the screws used to secure the
bracket to the servo.
|
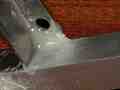
|
|
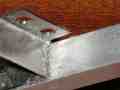
|
|
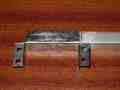
|
|
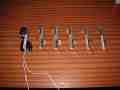
|
|