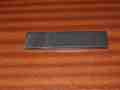
|
Make a bracket template
Cut a length of steel bar
|
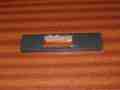
|
using the base of a servo as a guide, mark a rectangle in the steel bar.
Drill a small hole in each of the corners of the rectangle.
Using a small cutting disc cut the rectangle out of the steel bar. Try
to make the hole tidy and close fitting BUT it does not need to be
perfect because you will be finishing the template with epoxy putty.
|
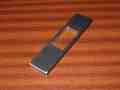
|
|

|
disassemble the servo
|
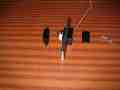
|
re-assemble the servo inside the cutout.
|
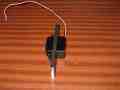
|
|
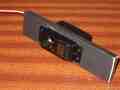
|
NOTE the servo does not fit exactly, there is a visible gap between the
servo and the steel bar.
|
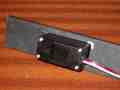
|
|
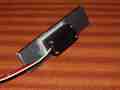
|
Fasion a small tool using some thin sheet steel (the same stock used
to make the brackets).
Mix some expoy putty and carefully FORCE it into the gap using the small
tool
|
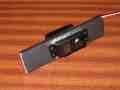
|
|
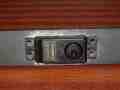
|
Using the holes in the servo guides, drill holes all the way through the
template
NOTE: these holes MUST be vertical since we want each hole in the
template to translate the hole from the servo shell to the bracket
without moving it relative to the servo shell
BEWARE: trying to drill too fast casues the hole in the servo shell to
become damaged (see top right hole). This was caused by the hot debris
melting and sticking to the plastic. Drilling more slowly overcame the
problem
|
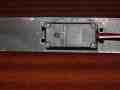
|
|
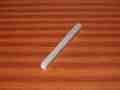
|
cut a length of extruded aluminium (square tube) to suit the size of the
servos. The length should be such that two servos will fit on it (length
on) with a small gap inbetween. A length of 100mm was selected so the
initial blank was cut to 105mm and both ends were trimmed to square ends
and a final length of 100mm.
|
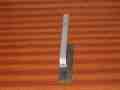
|
use the aluminium tude to mark the size of sheet steel blanks needed to
make the bracket.
NOTE the with of the blank is twice the with of the tube
|
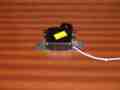
|
Use a servo to make the positions of the bends and cuts to be made in
the steel blank.
NOTE do NOT move servo while you are marking the position. That is, mark
one edge and without moveing the servo, mark the other edge. This will
give you a slight margin around the servo.
|
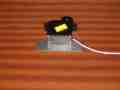
|
NOTE the blank is cut so that it is as long as three side of the servo
(the two shortest side plus one of the long sides)
|
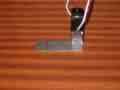
|
|
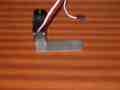
|
|
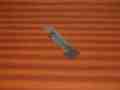
|
carefully cut along two of the lines as shown (using tin snips)
|
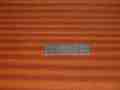
|
flatten the work piece using a hammer.
NOTE use small blows to lightly hammer the work piece flat, turning
the piece over and hammering the other side.
|
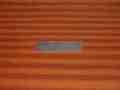
|
|

|
secure the work piece in a bench vice at the mid point (the line drawn
across the middle of the work piece)
NOTE: one end is completely within the jaws of the vice while the other
end is hanging slightly outside the jaws. Do NOT try to balance the ends
and have them both hanging out equaly.
|
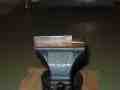
|
Bend the work piece along the mid point using the jaws of the vice to
form a sharp corner. Use a hammer to force the metel into shape. use
light hammer blows near the mid point NOT the edge of the work piece.
NOTE start with the end that is completely within the vice
|
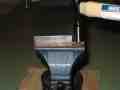
|
|
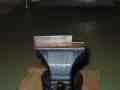
|
Repeat the process for the longer (middle) section
|
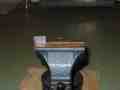
|
|
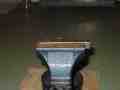
|
Slightly release the vice, slide the work piece across so that all the
edge is within the vice, re-secure and repeat the bending / hammering
process for the last section.
NOTE when you slide the work piece across be carefull not to move it up
or down of the next bend will not be in line with the first two
|
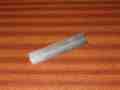
|
Remove the work piece and ensure that the sides are flat (you may have
bulges or dips).
If it is not square place the piece on a flat wooden surface and lightly
hammer it flat. You may need to turn it over hammer it on the other
side. This is easily done if you place the piece on the corner of a
wooden block
|
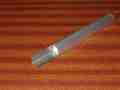
|
Place the aluminium blank into the steel blank and try rocking the
aluminium. If there is any movement the steel blank needs to be
corrected. put it back in the vice and VERY lightly hammer it along its
length to bend it more (close it). To open it, hammer it lightly on the
wooden surface.
If you open and close the steel blank too many times you will cause tiny
fractures along the bend. If the bend starts getting hard or changes
colour or if you can actually see small cracks. Discard the work piece
and start again.
NOTE if you put the work piece back in the vice, do NOT hammer on any
part that is NOT supported by the vice jaws (this will mean that you
will need to reposition the work piece). Do NOT take short cuts here.
|
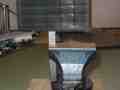
|
Secure the work piece in a bench vice such that one of the small marked
segments is above the jaws of the vice and the rest is below.
NOTE the work piece should be aligned so that the bend is vertical with
respect to the jaws of the vice.
|
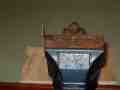
|
Very lightly pull the top of the work piece towards you.
NOTE the orientation of the work piece in the vice. you cannot pull it
if the vertical bend is face the other way.
NOTE when you pull the work piece do NOT apply force to either cornner
or the bend will NOT be straight (the work piece will twist).
|
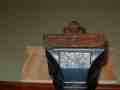
|
|
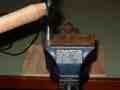
|
Finsish the bend by lightly hammering it into a sharp bend.
|
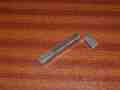
|
The work piece should sit flat on a flat surface. If it does not discard
the piece and start again.
|
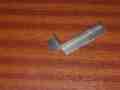
|
|
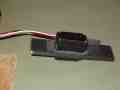
|
Place the work piece around the template as shown
|
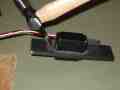
|
If it dose you fit properly you may be able to correct the problem using
a small pane hammer.
There is only so much you can do here. If the piece has twisted you will
not be able to fix it.
WARNING: If the piece does not fit reasonably well at this stage you
will have problems fitting the servo to the finished bracket with
machine screws (the gap between the walls of the bracket and the holes
that hold the screws will be too small and will NOT accomodate the nut)
|
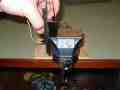
|
Holding the work piece and template together carefull place the work
piece in a bench vice. The template will be sitting on the jaws of the
vice. Carefully and slowly close the vice keeing the template vertical
and resting squarely on the jaws of the vice.
|
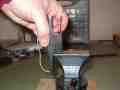
|
|
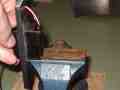
|
|
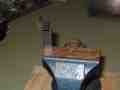
|
Remove the template. It should slide out easily. If it does not, then
you've done something wrong. Slacken off the vice and try again.
|
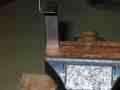
|
|
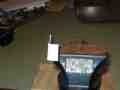
|
Again pull the work piece towards you.
|
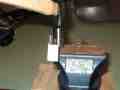
|
Again lightly hammer the bend to form a tight bend.
|
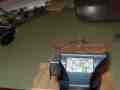
|
|
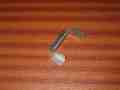
|
Remove the work piece from the vice and place it on a flat surface. The
edges should sit flat on the surface. If they do not and the fault is
EASILY correctable then try to correct it. If the piece is twisted it
may be impossible to fix. If so, discard it and start again.
|
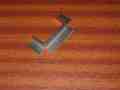
|
|
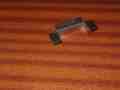
|
|
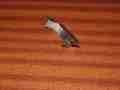
|
|

|
Place the work piece on the template. If it is not a good fit analyse
it, discard it, learn from your mistake and start again. You will
probably make several bad brackets until you get a feel for making them.
Persevere you will get there.
|
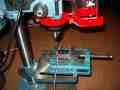
|
Secure the work piece and the template in a vice.
Mount the vice in the piller drill
Use the template holes as guides for the holes to be drilled into the
bracket
|
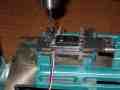
|
|
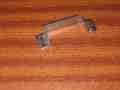
|
Remove the work piece and template from the vice and seperate them.
De-bur the new holes if necessary.
Check for flatness of the side pieces (you may need to hammer these flat
if the supports slipped while you were drilling)
|
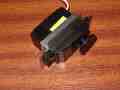
|
fit the bracket to a servo to ckeck it.
|
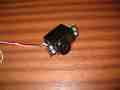
|
Fit the machine screws and nuts. Do not just fit the screws without the
nuts. There could be a problem with clearance of the nuts and you need
to check this.
NOTE when you fit the nuts do NOT tighten them until all the screws have
been fitted otherwise you could be mislead into thinking there is a
problem when there is NOT.
If the bracket does not fit properly analyse it, try to learn from your
mistake, discard it and start again. Do not be tempted to butcher the
holes to make it work. If the problem is with the template make a new
template. You will need to make many brackets and you want them all to
be reasonably similar, if you have to rework each bracket, each one will
be different and this will effect your robot. It will also take you
considerable time to rework each bracket, it will be quicker to make a
new template if the template is at fault.
|
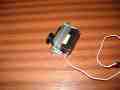
|
|
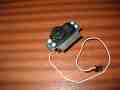
|
|
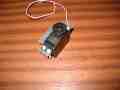
|
|
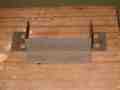
|
|
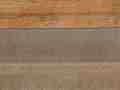
|
|
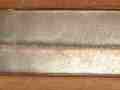
|
|
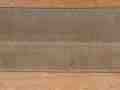
|
|
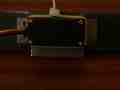
|
|
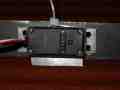
|
|
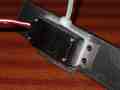
|
|
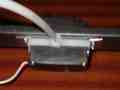
|
|
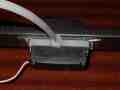
|
|
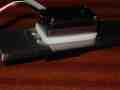
|
|
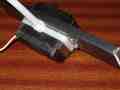
|
|
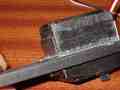
|
|
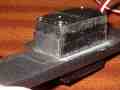
|
|
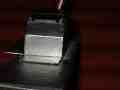
|
|
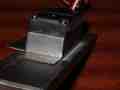
|
|
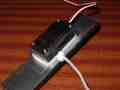
|
|
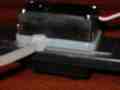
|
|
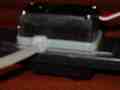
|
|
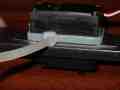
|
|
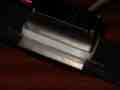
|
|
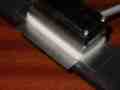
|
|
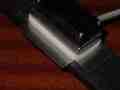
|
|
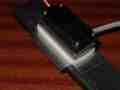
|
|
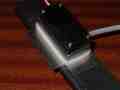
|
|
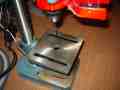
|
|
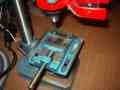
|
|

|
|
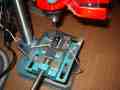
|
|
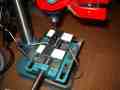
|
|
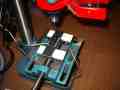
|
|
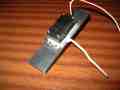
|
|
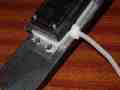
|
|
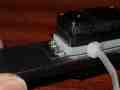
|
|
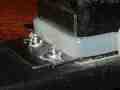
|
|
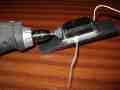
|
|
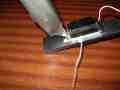
|
|
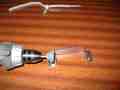
|
|
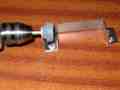
|
|
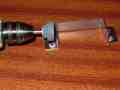
|
|
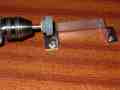
|
|
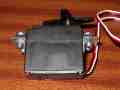
|
|
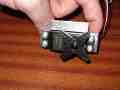
|
|
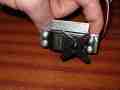
|
|
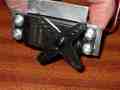
|
|